It's been three long months working hard on my Independent Research Project (IRP), but my final outcomes are now complete and my dissertation is all handed in! Which with only one more project left, scarily marks the fast approaching end of 3 years at university and the start of my career ahead. This blog is just a brief explanation of the practical work I've produced during my IRP and a chance for me to share my experiences of the project and also thank those that have helped me in my research.
Sketch of an original Greek sculpture
For those who don't know, my project has been based around classical sculpture, specifically focusing on figurative work. I have been investigating the development of sculpture techniques and processes by the Greeks and how artists are still using or adapting these skills today to produce work across a variety of industries, including Theatre and Film. My research has gone right back to looking at why the Greeks were so successful at recreating the human form and the development of their skills in carving in marble and casting bronze, right through to the new technologies that are being used today to produce sculptures such as CNC stone milling and even 3D printing.
As part of the historic research I have been exploring why Greek sculpture and the classical style has been so influential and highly revered by artists throughout the centuries, and what motivated the Greeks to become such perfectionists in recreating the human form, especially that of the athletic male figure. I've also looked at how the classical style has been reinterpreted, reproduced and copied by others such as the Romans or artists during the Renaissance. In fact most people do not realise that many marble sculptures that we think we know as Greek are actually Roman copies of bronze Greek originals that were melted down as scrap.
Then finally, I've also been interested in looking at the challenges a sculptor can come against with the use of new technologies and how the input of an artist may be affected by this. Also how vital is it to have a good knowledge and understanding of the human body and how it's made up in order to accurately recreate it and can a machine reproduce it as effectively as the tactile hand of a human.
The format of our dissertation allows a final piece and practical experimentation to count towards our final mark, which has enabled me to produce my own sculpture as part of the project. I was keen from the start to not just recreate an existing piece of Greek sculpture, but to draw, sculpt and create a new piece that was simply influenced by the classical style. Whilst the project has been about materials, processes and techniques, it has also been about exploring the skills and knowledge needed to accurately recreate the human form, and working from a live model has greatly helped me in achieving this.
The piece I produced was sculpted in clay which is known to be a very traditional material, but the casts I made were in modern materials that are commonly used in prop making today such as fibreglass and resin and also VAC forming. You can see below the sculpting and casting process I went through to produce my piece.
Just two days into sculpting.
After photographing my willing model, I was able to draw up my ideas for the piece and then begin sculpting in clay. Using measurements from the model, the clay is a half scale reproduction standing roughly 40cm tall.
It took me just 5 days to work on the piece, using my images and drawings as references along with my artistic licence to adjust and perfect the shape and posture. I was keen to recreate the 'contrapposto' pose that was a key style used in Greek sculpture, the gentle shift of weight through the body. I also wanted to create the idea of a broken statue just like an ancient piece that's not fully intact, so used broken pieces of plaster to indent into the clay around the arms and head, contrasting from the smooth surface of the main body.
I've always loved working in clay and really enjoyed the sculpting process and was pleased I was able to produce the piece so quickly. Below is the finished clay model, ready for moulding and casting.
Finished Clay Model
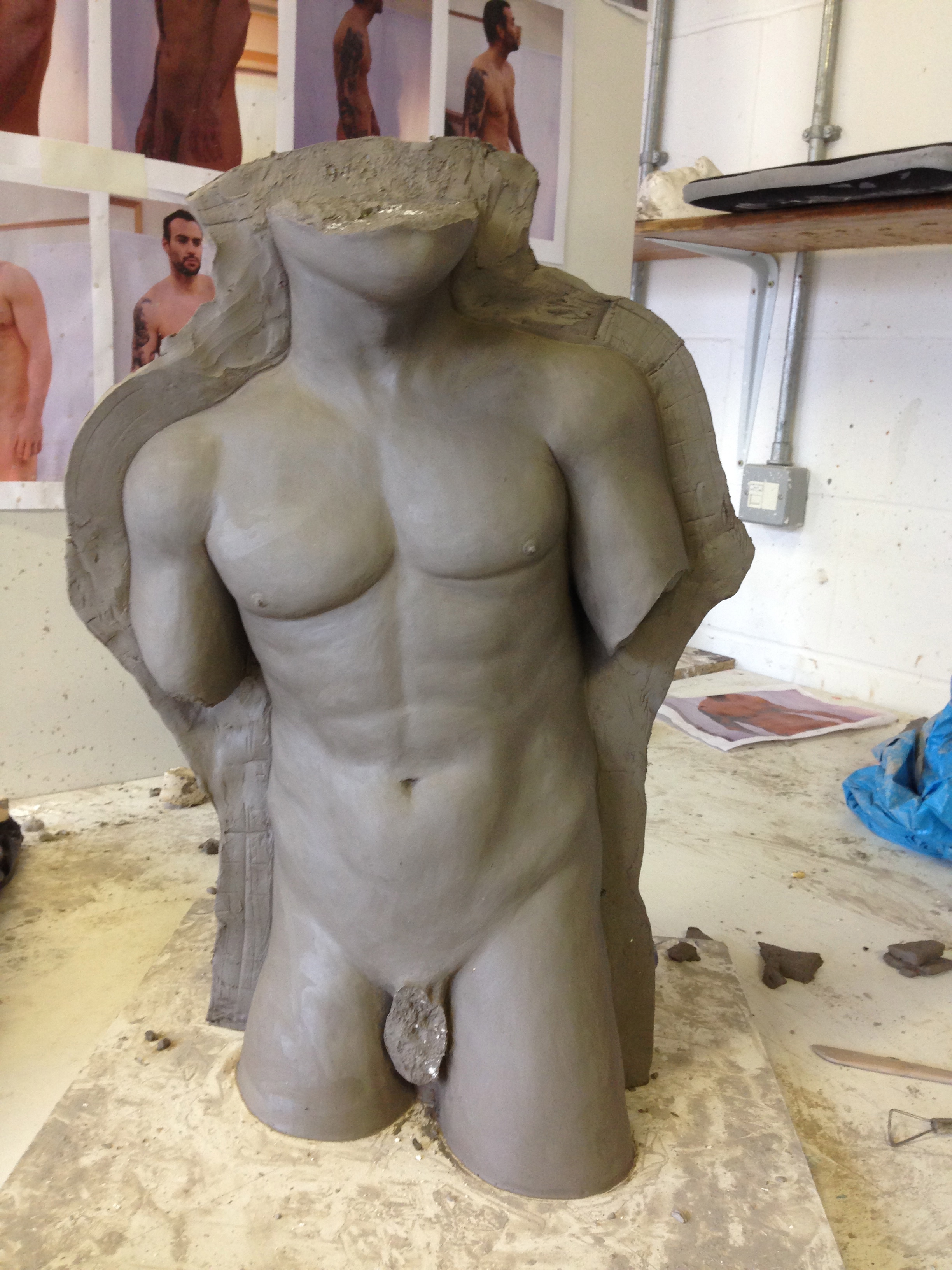
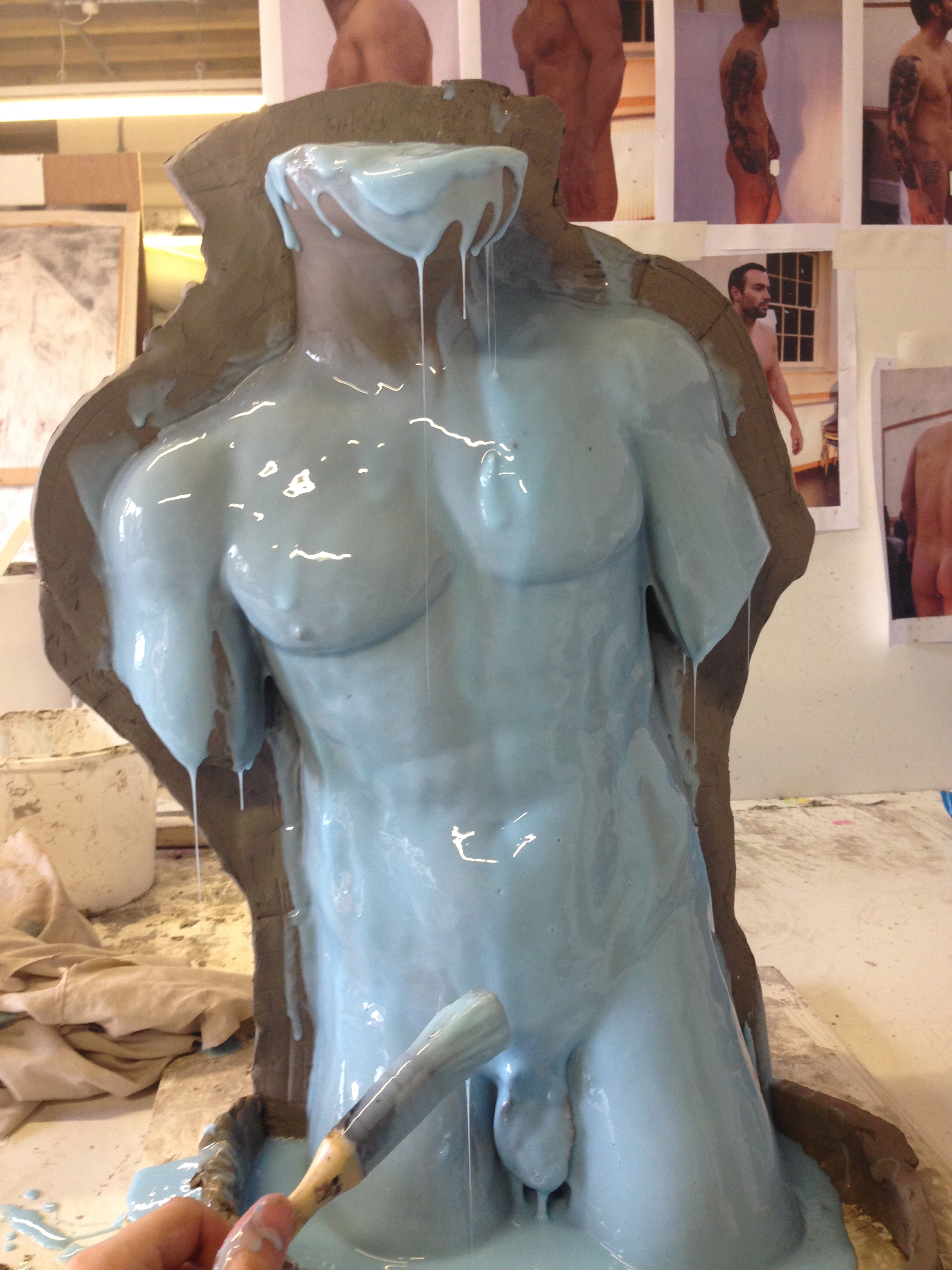
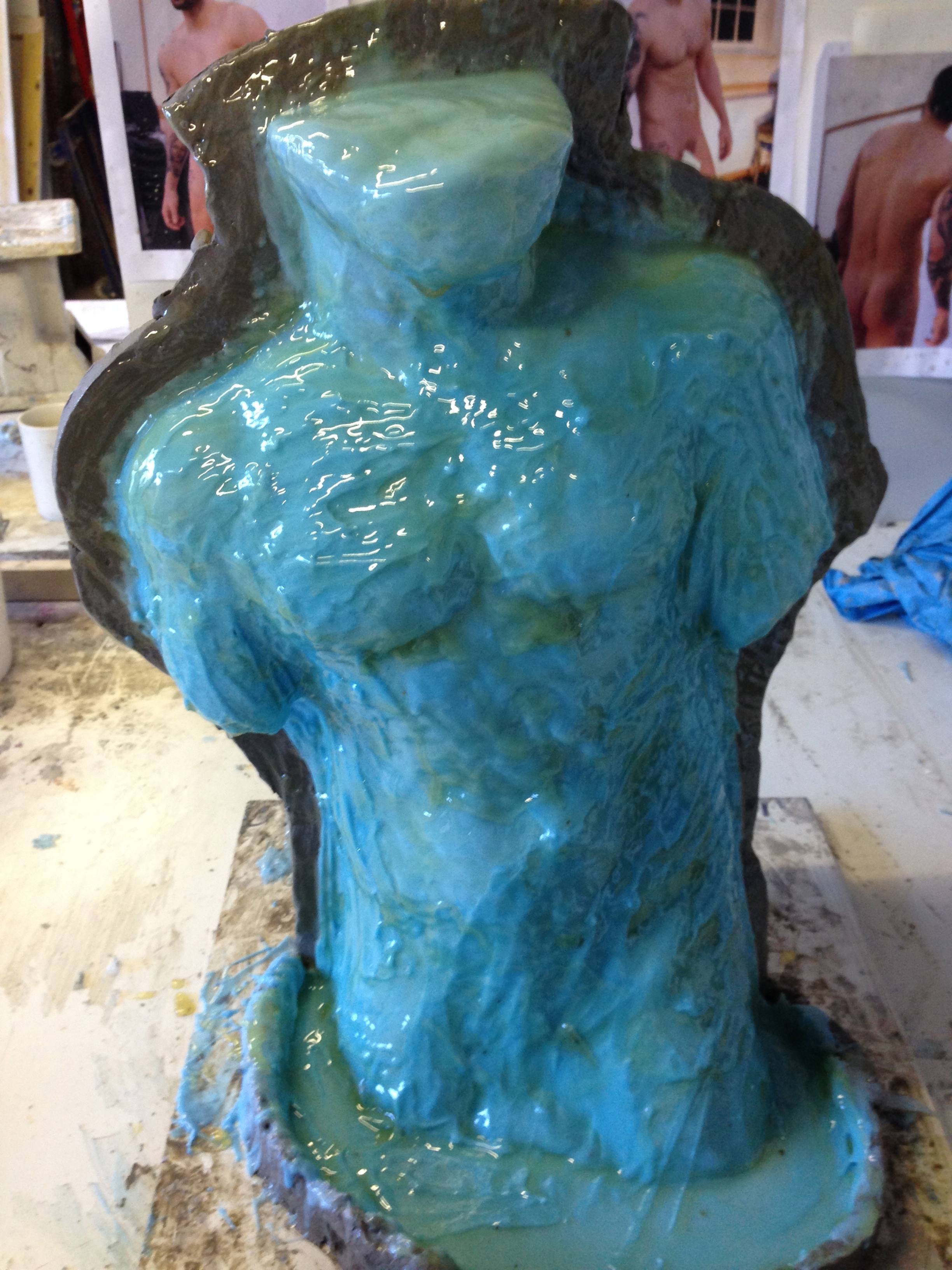
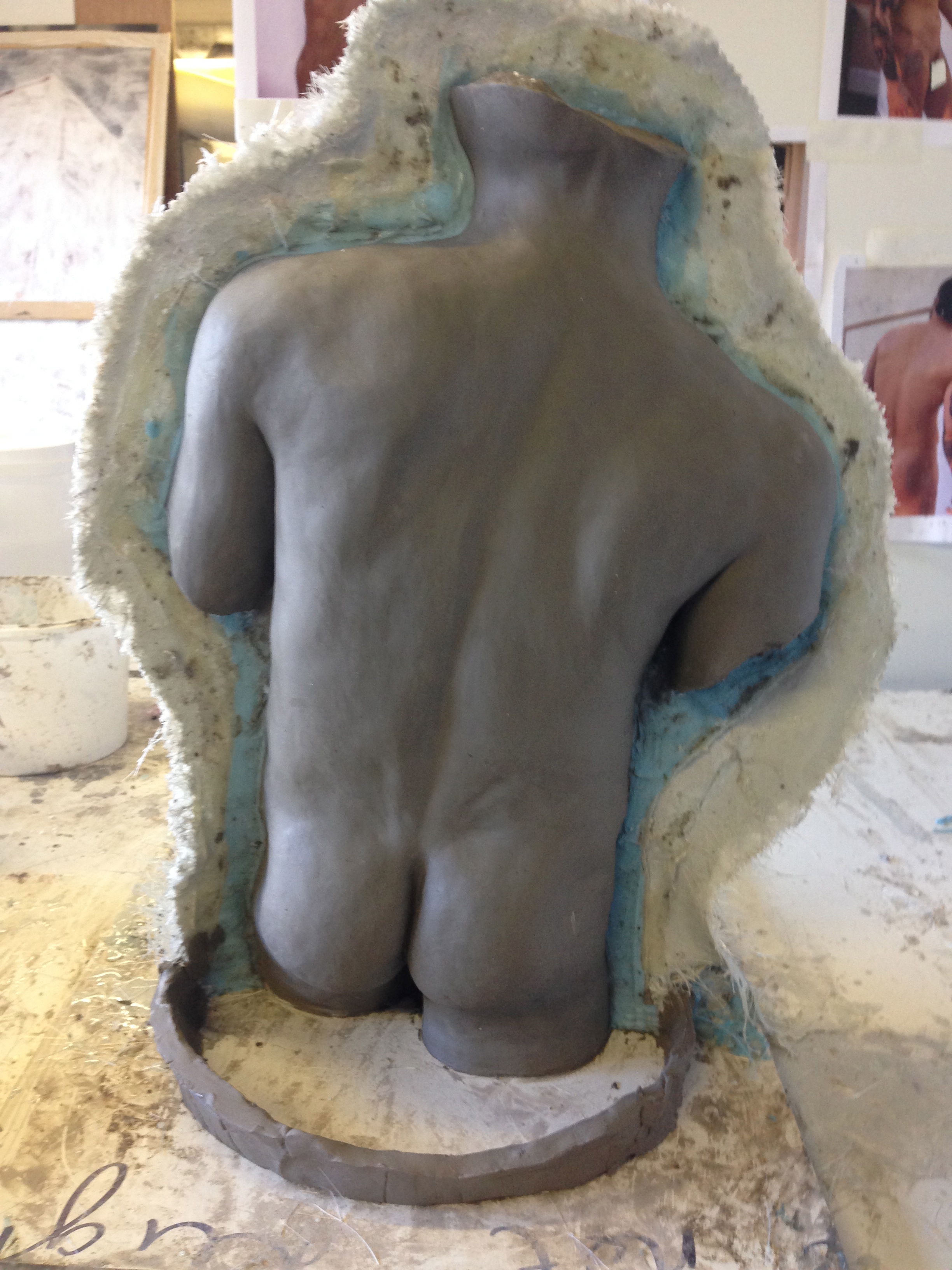
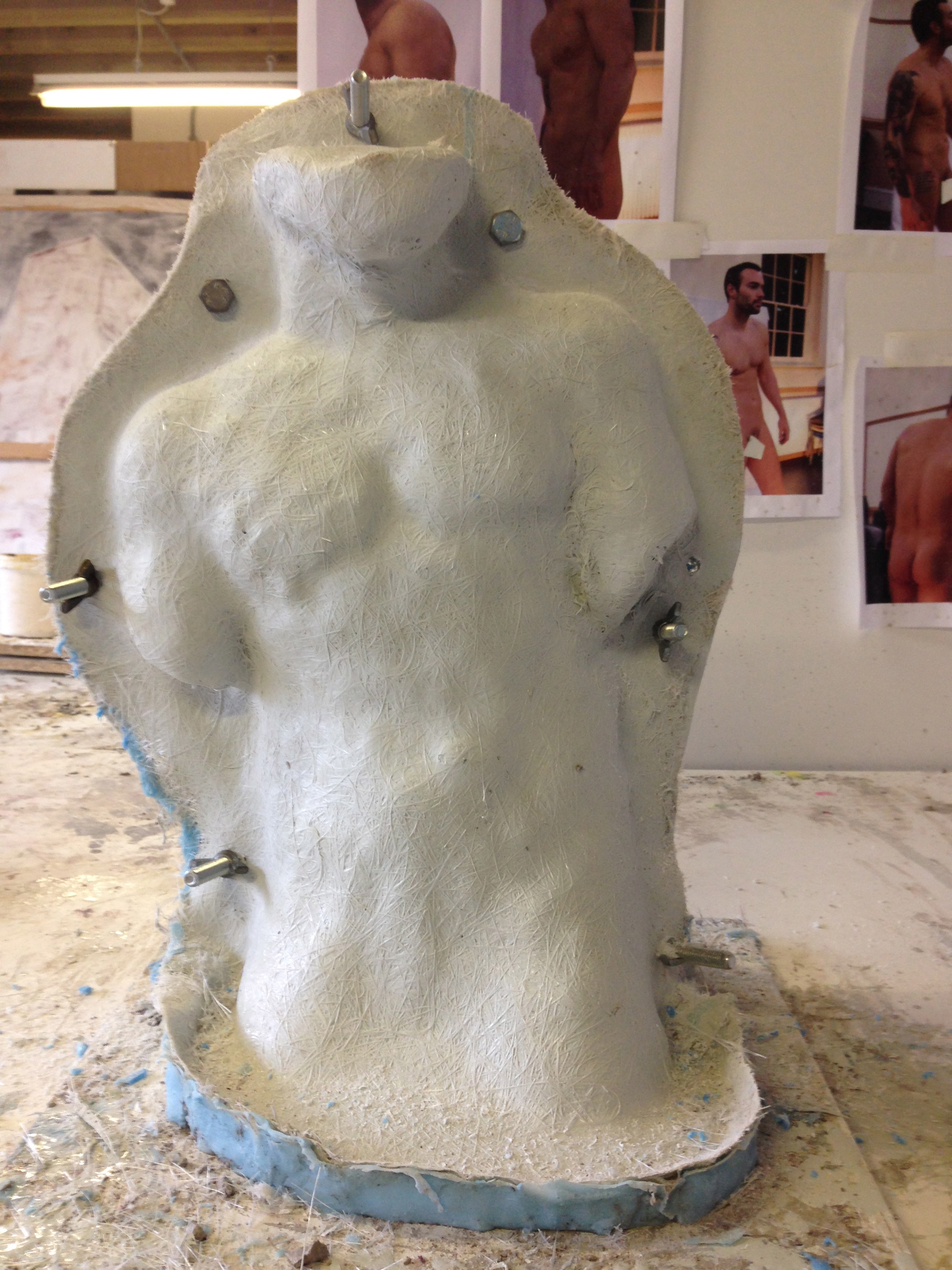
After finishing the piece in clay I was able to start the moulding process with a two part silicon mould and fibreglass jacket. Being the first time I had used silicon on this scale I was keen to experiment with the process in full.
The images here show how I split the model in half with a clay wall, allowing the first half to be moulded with liquid silicon, brushed on and allowed to set. Then the addition of the fibreglass jacket to strengthen the mould and hold the silicon in place. Once the front half was complete the process was repeated for the reverse half until the two part mould was complete. The fibreglass jackets must be bolted together to ensure they sit together well during the casting.
The first casts I took were simply in plaster and as two separate pieces to allow me to use them for a VAC forming outcome which you can see below. I then cast two separate outcomes, firstly one in resin and fibreglass and the second in solid jesmonite with marble powder in the surface layer. Both outcomes were begun by laying up the two halves of the moulds separately, the fibreglass outcome using gel coat resin to pick up the detail and the second with a thick jemsonite and marble powder layer to do the same. Once set the two halves were joined together in the mould, with the fibreglass and resin being strengthen on the inside along the joins and the jesmonite simply being filled up solidly, using a cheaper filler to also bulk out the jesmonite.
The fibreglass is hollow on the inside and has been painted to finish it off and give the impression of a stone sculpture. The jesmonite is solid and I was able to polish up the surface and reveal some of the marble powder giving it a really effective look. The surface also had a few natural cracks that I left as part of the piece and I chose not to paint into this outcome as the jesmonite had a strong quality to it already.
Resin and Fibreglass Jesmonite
Carving in Parian Marble with Pat Rae
As part of my research through the project I have been hugely lucky in being able to talk to various professionals and also companies that produce sculptures in various mediums and for different purposes, all who have influenced and helped me to reach my outcomes. Below I have noted those that I have been in contact with and would like say a thank you again for the time given over to speaking to me and for helping build my research.
With a specific thank you to the wonderfully skilled sculptor Pat Rae, who kindly taught and let me work in actual Parian marble. Under her careful guidance and over just three days I was able to produce a small outcome and learn just how hard it is to carve in marble. This was a brilliant addition to my project and I was very grateful for the chance.
Pat Rae - www.patrae.co.uk
Links to other professionals I have spoken to:
Steven Hunter - www.stevenhuntersculptor.com
Aden Hynes - www.sculpturestudios.co.uk
Peter Evans Studios - www.peterevansstudios.co.uk
J. Rotherham (stone CNC milling) - www.jrotherham.co.uk
CNC Polystyrene - www.cncpolystyrene.co.uk
Elinor Wynne Lloyd - It's All Greek - www.itsallgreek.co.uk
I have really enjoyed this whole project both in the research and outcomes that I've done. Being able to spend a lot of time producing a final piece from start to finish has been a good learning curve and has allowed me to progress my skills in many areas. It has been great talking to professionals and meeting people through the project that have shared their skills and knowledge to me and helped with my research. And the project has spurred me on to experiment further with creating sculpture and I will hopefully get the chance and time to produce more work in the future.